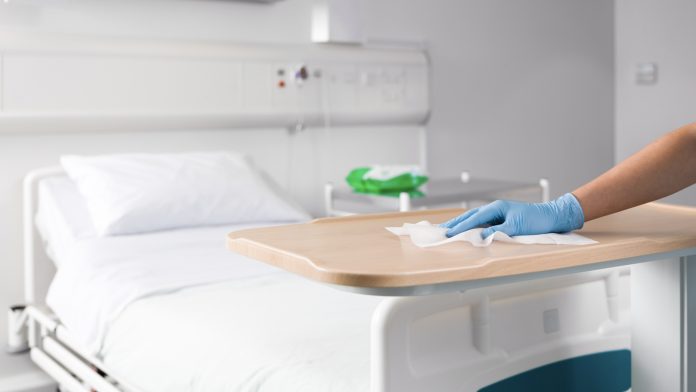
Infection prevention & control (IPC) is an evidence-based practice with conversations regarding topics like surface disinfection products, hand hygiene and patient isolation.
IPC thought leaders are always considering key factors that influence what products to use within healthcare. However, one factor is often overlooked but just as important as the other factors mentioned—material compatibility.
It is vital that disinfectant products are appropriately tested for material compatibility to avoid damage to medical equipment, increasing overall costs and spreading infections. If the equipment has not been appropriately tested against disinfectants, repeat exposure to these chemicals can cause cracking and critical failure of hospital surfaces and equipment.
What is material compatibility?
Material compatibility tests a material’s resistance to corrosion, staining or rusting when in contact with specific chemical agents. It is essential to test hospital equipment against disinfectant formulations as incompatibility between the two can lead to stress cracking and brittle fractures on equipment. These cracks in equipment can provide a reservoir for microorganisms, protecting them from further disinfectant use, which can increase the risk of infection.
Equipment in healthcare can be made of a variety of different materials, such as metal or plastics (plastics and polymers being an umbrella term for hundreds of different chemical structures). Each plastic will have different physical properties, such as strength, flexibility or thermal resistance, depending on the equipment’s function. Subsequently, each plastic will have a different level of resistance.
Regulations on disinfectant products
Before disinfectant products are allowed to market, they must adhere to regulatory standards that focus on their efficacy, stability and safety. This makes choosing the right disinfectant a crucial part of any IPC strategy. Currently, there are three categories of wipes:
- Detergent wipes for cleaning visibly soiled areas
- Disinfection-only wipes for disinfection after cleaning
- Combination detergent-disinfection wipes for the one-step removal of organic matter and reduction of microorganisms
Despite each of these categories having their own benefits, there is now evidence that show the benefits of using disinfectant products and detergents in a ready-to-use wet wipe1.
Medical devices
While disinfectants are held to regulatory standards, these standards do not apply to the manufacturing and construction of medical equipment. Unfortunately, in recent years manufacturers have moved away from using durable metals and plastics in favour of cheaper materials. This change has increased the risk of damage from chemical agents such as chlorine, alcohol and hydrogen peroxide (all common agents found within disinfectant products).
The problems of poor compatibility
Most manufacturers understand the need for material compatibility and incorporate materials with high resistance against disinfectant products, but that can’t be said for every piece of equipment within a healthcare setting.
Certain pieces of equipment can have residual internal stress because of the moulding and manufacturing process, which can result in cracking when damaged by chemical disinfectants.
To reiterate, the need for thorough material compatibility is paramount for both IPC and financial incentives. In the UK alone, healthcare-associated infections costs NHS England £2.7 billion and 62,500 days of frontline-worker absences per year.2
Environmental stress cracking
Environmental stress cracking (ESC) refers to the premature initiation of cracking and embrittlement of a plastic caused by simultaneous stress, strain and contact with a specific fluid.
ESC is a physical process with highly localised plasticisation (the process of changing the structure of a polymer to make it easier to bend) and stress-enhanced fluid absorption. For a moulded component, the stress does not need to be applied; it can be as a result of the moulding/forming process.
Brittle fractures
Brittle fractures can occur in plastics that have been affected by environmental stress cracking. These cracks can appear on medical equipment and are an indication of sudden, catastrophic failure. A good example of a brittle fracture would be evidenced in the video below:
Choosing the right disinfectant
Disinfectants need to be compatible with equipment used within healthcare. When choosing the right disinfectant product, there are a few factors you must consider:
- Efficacy– Take into consideration both the formula and the wipe substrates’ ability to kill and remove microorganisms. Should the wipes be of poor quality, they might interfere with the wipes’ ability to trap and kill microorganisms.
- Compatibility– Looking at a disinfectant’s compatibility can help you ensure that your equipment will not be damaged. Damage can increase the risk of infections by allowing equipment to harbour microorganisms in cracked/damaged equipment for example.
- Contact times– Using a product with realistic and practical contact times helps maintain good IPC practices and allows staff to effectively clean surfaces and equipment.
In summary, choosing the right disinfectant is vital to any IPC strategy. By reading manufacturing guidance and disinfectant compatibility matrixes to find a good fit, you can ensure your equipment is being cleaned effectively and not being damaged by disinfectant agents within products.
References
- Rutala WA, Weber DJ. Disinfection and sterilization: An overview. Am J Infect Control. 2013;41(5):S2-S5. doi:10.1016/j.ajic.2012.11.005
- Guest JF, Keating T, Gould D, Wigglesworth N. Modelling the annual NHS costs and outcomes attributable to healthcare-associated infections in England. BMJ Open. 2020;10(1):e033367. doi:10.1136/bmjopen-2019-033367
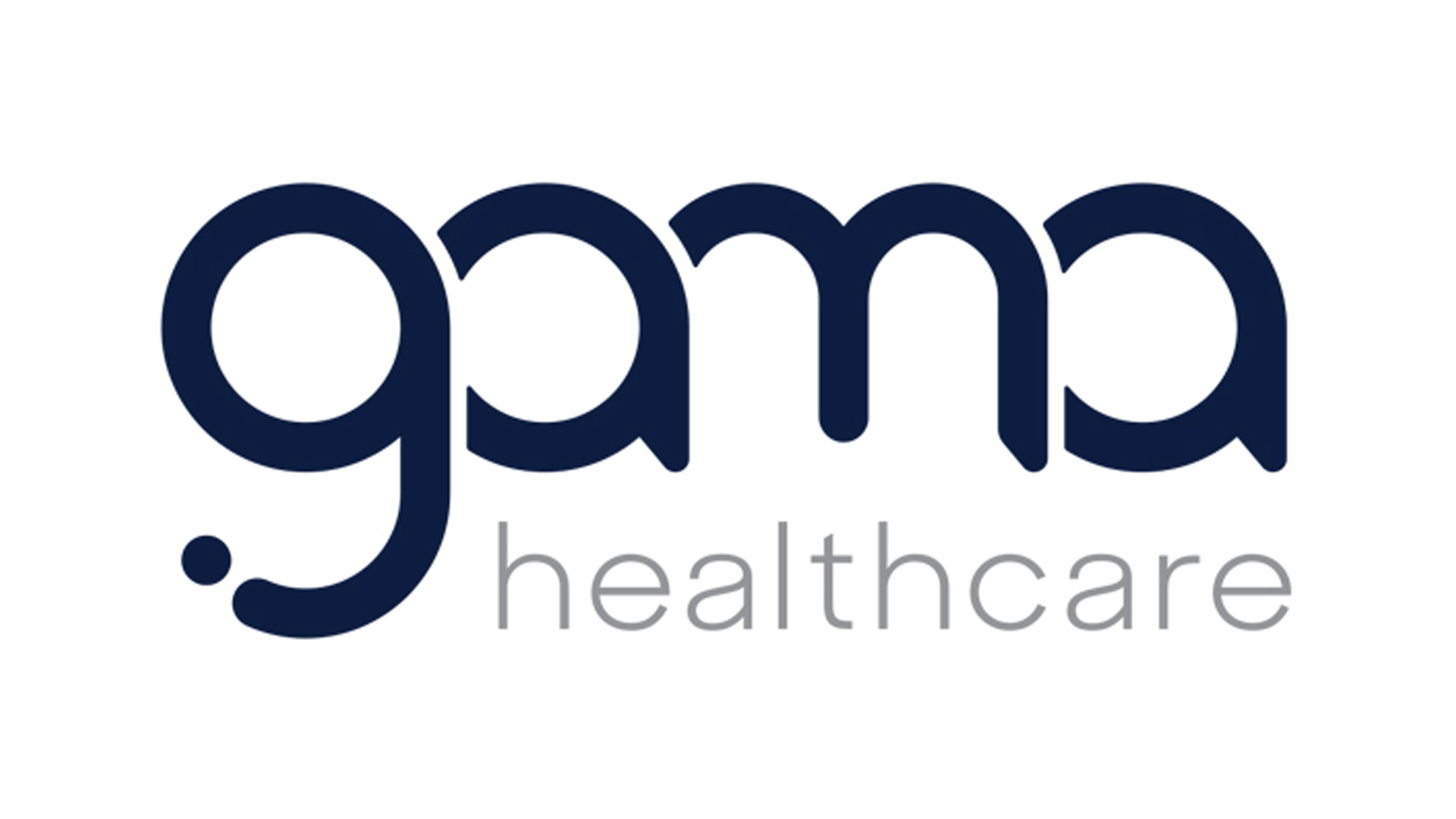