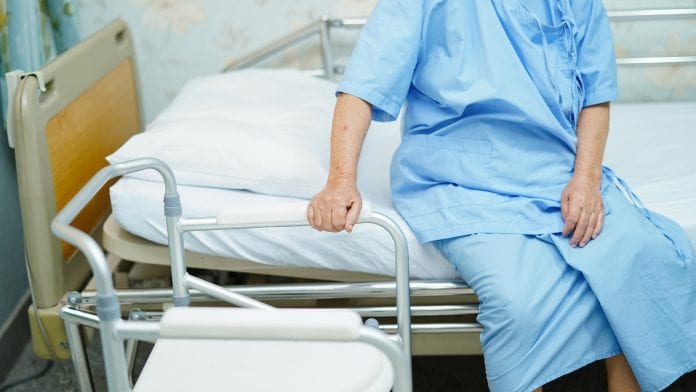
As infection prevention teams map their sites’ cross-infection pathways, Haigh and others help to simplify the waste disposal process.
While COVID-19 dominates the headlines, healthcare-acquired infections (HAIs) continue to cause mortality worldwide, with substantial associated costs. The US Centers for Disease Control and Prevention (CDC) estimates that HAIs cause around 100,000 deaths per year and over $9.8bn in related costs. Of these, Clostridium difficile (C. diff) infections alone make up 15.4%, averaging over $11,000 per case. The ability of Clostridium spores ability both to withstand heat and certain sanitisers and to survive in fine scratches on surfaces increases the challenge. One study found that temperatures over 80°C actually increased reactivation of dormant C. diff spores.
Human waste management, including the use of bedpans (‘utensils’), bottles and bowls, is a key aspect of infection prevention and control (IPC). Human stools contain around one trillion distinct microbes; and evidence of SARS-CoV-2 has been found in faeces for over two weeks after infection. Care environments typically include both patients with contagious diseases and patients with reduced immune systems, so site processes should be designed to minimise cross-infection pathways – specifically, used utensils must be thoroughly sanitised between use, or a new utensil must be used each time.
Operational details to allow clinicians peace of mind
Clinicians understand the importance of reducing the risk of HAIs, as this can have benefits for patient outcomes, bed occupancy, proportions of staff time spent caring for patients, and overall medical expenses.
Aiming to provide clients peace of mind, Haigh, a UK-based specialist, approaches the infection control challenge systematically: identifying sources of risk, mapping physical pathways through site, analysing the time, points of contact, and crossing pathways, and guiding clients on possible improvements. This mindset is embedded in the company’s product designs – including that of the Haigh Quattro and Haigh Solo bedpan disposers (also called ‘macerators’) – where the disposable utensil system, simplicity of use, and equipment uptime were identified as key.
Haigh anticipates that investment in IPC will continue to increase, including in elderly care and the private sector. Patients and their families, insurers, and other forms of payor are acutely aware of the merits of a hygienic environment. Indeed, a new challenge arising for healthcare managers is choosing whether to optimise site IPC processes within their existing structure, or to make structural improvements, despite the effort, precisely because of the current situation.
Process compliance by design
Simplicity of use enables busy staff to follow appropriate clinical infection control processes. For example, the entire utensil disposal process can take the user just eight seconds. The Haigh Quattro is hands-free to open, the user is presented with a clean, stainless steel hopper; then they place used utensils inside, press a pedal to close it, and can leave. Boxes of new disposable utensils can be positioned where appropriate on site, for example near the point of use rather than in a sluice room. Clinical staff can have confidence that a fresh, hygienic utensil is used every time.
Infection control through better uptime
Designing processes to maintain hygiene is only part of the challenge for infection prevention and control teams. They must also consider what needs to be done if something goes wrong.
Haigh has observed that its clients look for systems which are easy to implement, easy to train staff in new processes, reliable, and easy to maintain. Reducing the number of utilities which are essential to operation means the process is more reliable and less vulnerable to system failure: Haigh’s bedpan disposers typically need just cold water, with no need to connect to a hot water supply or provide sanitiser refills.
Minimising non-essential movement
One non-clinical area often identified for improvement by Haigh’s analysis is operations and waste collection staff. Non-essential movement around a site contributes to the risk of cross-infection.
Healthcare operators must consider not just the risks to patients, but to staff and business continuity as well. In a recent report, a third-party collection provider noted the challenges its staff have faced with COVID-19 until all employees are vaccinated. Implementing bedpan disposers avoids the need for utensils to be collected in bins, helping to reduce janitorial movements.
Creating an evidence base, site by site
Healthcare operators often recognise the benefits of disposable utensils, but lack the bandwidth to deliver a full project until a base of evidence specific to their sites becomes available. However, the growing usage of disposable systems means that there are now low-risk approaches: in most regions it is possible to purchase small quantities of disposables, without ongoing commitment, capital expenditure, or change to infrastructure. A box may contain 100 to 500 utensils: enough for a small team to trial with temporary processes.
“New clients would benefit from trying kidney dishes first,” explains David Meek, Global Healthcare Education Specialist at Haigh Engineering. “The contents often do not need special disposal procedures; they are easily shipped around the world which helps with procurement; and clinicians can quickly get a feel for the product quality. Once site staff understand the benefits, it is easier for infection prevention and control teams to make an evidence-based decision.”
Existing infrastructure, such as automatic washers, can be complementary. Used disposable utensils are placed in bins or specialist disposers; while a smaller range of multi-use formats allows less changeover of washer racking, further freeing up staff time for care. Once sites have more experience, disposal units can be installed, further shoring up clinical hygiene standards and long-term financial benefits.
After a trial with bedpans and bottles, a leading healthcare provider reported significantly lower antibiotic usage at site after introducing disposable bottles, with E. coli cross-infections being the biggest change. Where bottles previously were kept until the morning, to avoid the noises from washing waking up their clients, the new approach allowed hygienic disposal instantly.
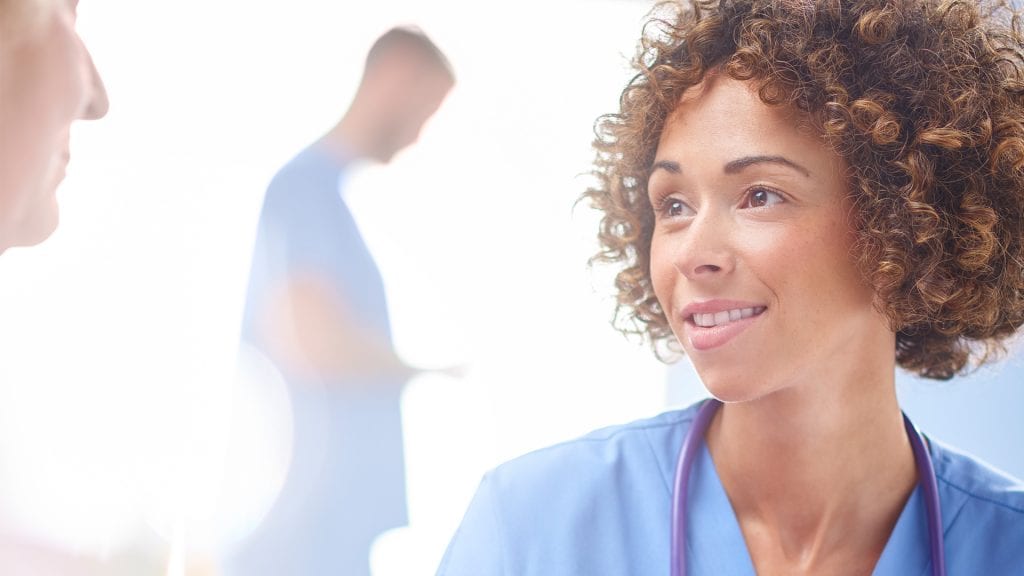
Around the world
A wide range of pulp qualities exist to meet different site specifications and budget.
Demand in the Middle East for the highest quality versions led Saudi firm Al Kifah ICS, the infection control specialists, to develop its range of white pulp products for a soft, clean look, while maintaining necessary water retention properties.
Many countries have stringent environmental standards, though few push them as far as Italy. Promos SpA, an Italian manufacturer of disposable healthcare utensils, worked closely with regulators and customers to meet stringent environmental controls – both at the company’s production facility and in their clients’ wastewater management protocols; as water quality must be high, with a minimum of harmful chemicals. Alongside infection control concerns, system uptime is of similar importance to ensure that waste is disposed of through an approved channel. The Promos SpA team is focused on its ongoing support for customers, and rapid response.
In Germany, manufacturer Bosk GmbH ECOPATENT® has spearheaded client education on the benefits of disposables. These benefits are now well understood by healthcare providers across the country, and the company has worked through the practical hurdles of meeting wastewater quality targets.
AMG Medical Inc, a medical supplies specialist, has developed a reputation for service: both providing wholesale medical products, and with after-sales care for clients across Canada. Recently the team delivered a first-in-Canada integration of MedPro Defence by Haigh Quattro disposal units with the building automation system, allowing the flagship new hospital better monitoring of system uptime.
The common theme of all these use cases has been their choice of Haigh as a partner for quality bedpan disposers.
Environmental considerations
Water: a typical disposal unit uses 24l of water or less for up to four standard utensils, with no need for heat. In contrast, before converting to disposables, Haigh’s outreach team found one site using 60l or more of hot water in a tap-based rinsing process. Across a whole hospital, the difference adds up to swimming pools of hot water.
Chemicals: dosing can be a specific decision, not a requirement. In a hospital wing with 20 inpatient beds, there can be a hundred uses per day, or 36,500 per year. For a cleaning process that uses 20ml of disinfectant per utensil, this adds up to 730l per year – or up to 36.5 cubic metres across a hospital of 1,000 beds. With disposables, new utensils are clean out of the box with no need for disinfectant. In addition, less disinfectant is washed into the water system.
Plastics: disposable utensils are typically made with wood pulps, such as from recycled paper. Bedpan disposers break the pans into fine particles, mix them with water, and empty the slurry via a drain. The machine rinses itself, to be clean for the next use. For sites still using single-use plastic utensils, there is potential for major reduction in landfill.
Increasing support for healthcare providers
“For healthcare providers, the support network for disposables is becoming mainstream,” Meek notes. “The wide variety of pan formats on the market makes it relevant to multiple ward types, from palliative care to trauma, so the one system can be adopted across a whole site. Suppliers are trialling maceratable wipes, both wet and dry formats, to simplify further the waste pathways: wipes can be placed in the disposal unit along with pans and their contents, all in one movement. With sales growing worldwide, Haigh is delighted to support clients through their current and future challenges.
“For example, when the UK’s Nightingale hospitals, which provided emergency ICU capacity, were planned and constructed, they chose disposable utensils for bedpan management, with disposers fitted where they were needed. Haigh and its partners look forward to working with ever more clients worldwide, helping improve infection management in these challenging times.”
This article is from issue 17 of Health Europa. Click here to get your free subscription today.
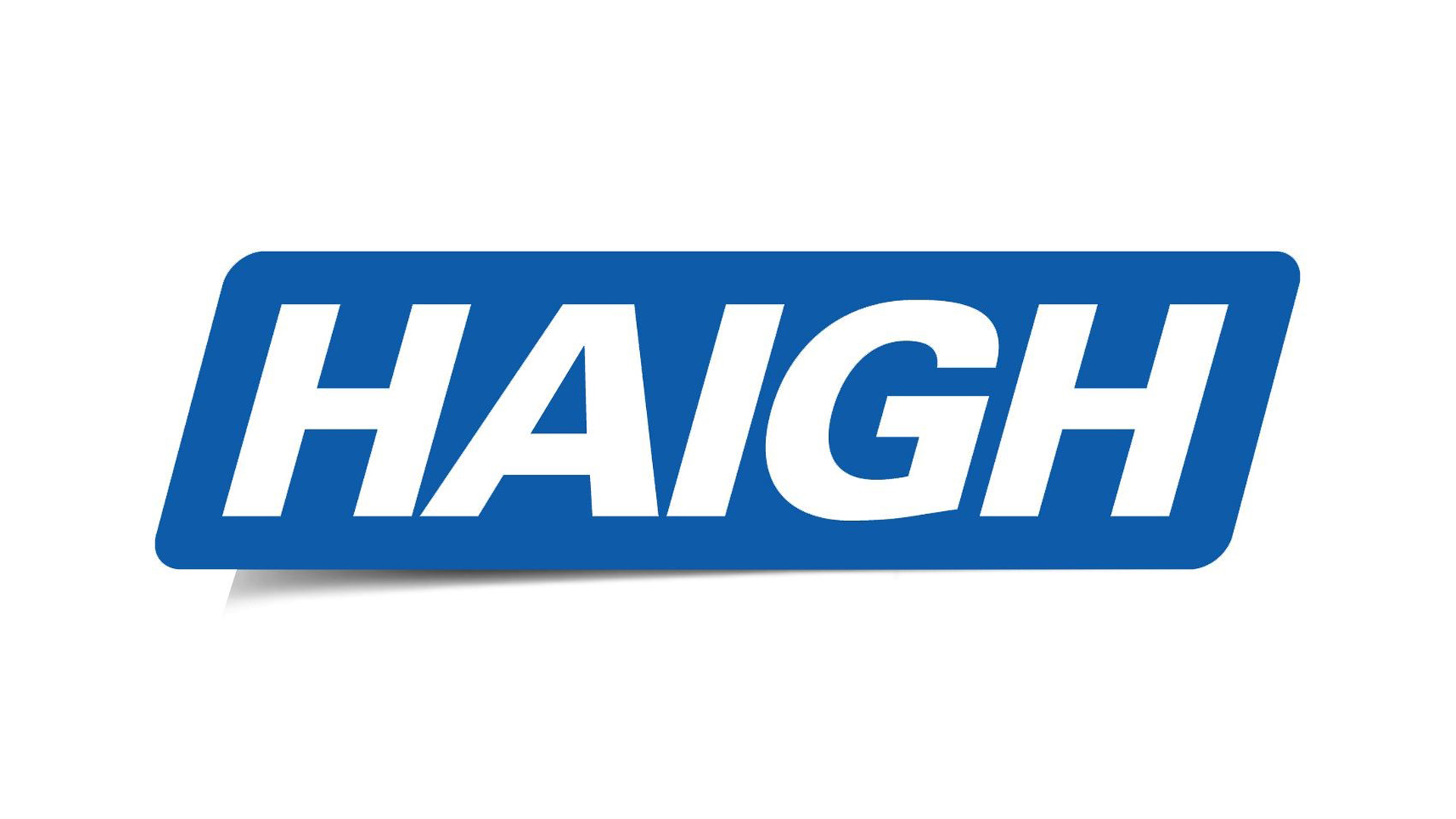