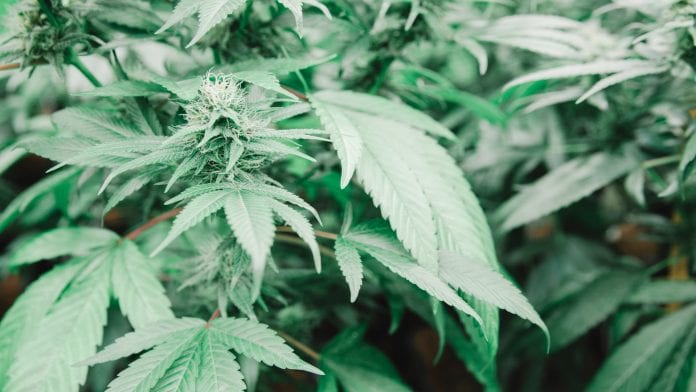
Cannabis growers, SANlight Solution GmbH, develop their business with a partner that understands sustainable cannabis growth and technology.
Cannabis and its use by humans dates back more than 5000 years in recorded history and even further back according to archaeological evidence. Its value as a cultivated plant ranges from fibre and rope, to food and medicine and – due to its psychoactive properties – religious and recreational use. Over the course of time, the misuse of cannabis as a psychoactive drug has resulted in a worldwide prohibition.
An introduction to the challenge of transferring cannabis products to broadly accepted phytopharmaceutical products
Despite this, the pharmacological usefulness of cannabis has continued to be revealed over time. Cannabis is often used a generic term to denote the several psychoactive preparations of the plant Cannabis sativa and Cannabis indica or its hybrids. The major psychoactive constituent in cannabis is ∆-9 tetrahydrocannabinol (THC). Compounds which are structurally similar to THC are referred to as cannabinoids. In addition, several recently identified compounds that differ structurally from cannabinoids nevertheless share many of their pharmacological properties. Cannabidiol (CBD) is another well-known constituent of these plants and the focus is also increasingly on the terpenes which are organic compounds for medical use.
Although there is a long tradition of the use of cannabis, it seems that the pronounced use of THC as a worldwide prohibited intoxicant has limited its use as a well-recognised medicinal plant. This has changed in recent years, and there is an enormous effort to position cannabis in the phytopharmaceutical industry and also to legalise recreational use.
Today, the focus is clearly on the pharmacological effects of cannabis. CBD is valued as an effective and natural pain reliever with impressive advantages over pharmaceutical products. Cannabidiol is known as antispasmodic and anti-inflammatory and due to its natural composition, the side effects for the patient are less prominent than comparable chemical substances. It has also been shown that cannabis can help with nausea, depressive mood and insomnia. Furthermore, taking CBD can increase concentration and diseases such as hyperactivity syndrome or ADHD can also be treated. Finally, a few fully approved THC enriched phytopharmaceutical products are prescribed by trained doctors.
Overall, the natural ingredients of cannabis have a number of positive effects whereas research into the efficacy of the medical use of cannabis drugs is still in its infancy. The effects are to a vast extent still not sufficiently proven by scientifically executed studies.
There are many ‘hands on’ applications, but still very little clinical trials that demonstrate quality, safety and efficacy. This handicaps the authorisation of cannabis as a medicine by legal authorities and health insurers, who are reluctant with cost compensation. However, at the same time, it is a perfect outset to enrich the existing phytopharmaceutical industry with a solid and distinguished cannabis-based supply chain. Furthermore, we see a future oriented discussion to establish a legal framework for the production, trade and use of THC and CBD cannabis in both developed and in developing countries.
Two companies. One motivation. SANlight and SANlight Solution are driven by nature
SANlight was officially founded by two university alumni in the Austrian mountains in 2011. Their sound technological background combined with their green fingers put them in the perfect position to develop highly innovative illumination solutions for horticultural applications. From the beginning the emphasis was exclusively on solid-state light sources combined with smart electronics and sensors. An innovative and forward-looking approach was required to focus on the high-end B2C market for the early years, which not only awarded this a self-financed and profitable company growth, but also a customer centric product development cycle – with broad and rapid user feedback via then emerging social media channels.
Today, SANlight is illuminating more than 75,000 indoor and greenhouse facilities all over Europe and is operating its own multi-level indoor grow lab within 250m2 at its headquarters in Bludenz. Linked with strong collaborations with research institutions in Germany, Switzerland and Austria, the focus today is not only on illumination but also the engineering of effective grow facilities. “In our almost 10 years of operation, the activities of SANlight have expanded from better light for better plants all the way to grow solutions truly driven by nature” says David Schmidmayr, one of the founders.
What is so special about the illumination gear of SANlight? “We always put ourselves in the position of the crop, carefully considering the five major external growth parameters with illumination being only one of them. This holistic approach towards plant growth was, and still is the key to our success,” says Martin Anker, the other founder of SANlight. This clear commitment to work on system solutions triggered in 2018 the foundation of the SANlight Solution GmbH – a company serving the professional horticulture industry as a solution provider for illumination and plant production.
Effective and healthy growth – the interaction of many parameters driving illumination to be a force of innovation
The growth process of a crop is determined by its primary and secondary metabolism. Light emitted in the photosynthetic active region (PAR – ranging from 400-700nm) of the daylight spectrum is commonly seen as the driver for the build-up of biomass. The healthiness is heavily determined by the internal signals sent from various photoreceptors. These receptors are sensitive in a selected region of the daylight spectrum ranging from the ultraviolet (UV-A), visible or infra-red regime. With its spectral sensitivity the receptors are triggering different internal signals depending on the light intensity. And there is an interdependency of signals coming from different receptors. Without going into more detail, we can already see quite some complexity here.
The fact that the interaction of the provided light with the availability of nutrients, the water uptake from the roots, CO2 concentration in the air as well as humidity and temperature are in addition to the spectral composition and intensity of the illumination – but do not forget that a plant does usually also require a period of darkness to steer its inner clock or circadian rhythm. Therefore, it becomes obvious to the reader that the holistic approach of SANlight mentioned above requires quite some competence, but at the same time reveals a lot of potential to optimise the grow process of plants.
One early conclusion that has been drawn by the SANlight research team back in formative years is that the use of selective colours only in the blue and red spectral regime (within the PAR region) is a good basis, but certainly not sufficient for modern cannabis cultivation. We have added greenish and far-red spectral signals to compose a well-balanced and broad ‘sun like’ emission. The relative intensity of the different spectral regimes has been optimised over various grow cycles. We clearly distinguished the spectral distribution of the different grow stages of the cannabis plant. The spectrum for the mother plant nursery is designed to keep the crop healthy and strong for the retrieval of cuttings and at the same time avoiding pullulation – even worse – blooming.
The spectrum for the rooting of cuttings or the epitaxial growth from seeds needs to be designed carefully to generate resilient young plants. The illumination of the vegetative phase is designed to develop the young plants to pullulation with a strong focus on a concerted transfer into the generative or blooming phase where the red and far-red regime of the spectrum is in the focus. However, at the same time the spectral distribution was carefully optimised to maintain sufficient freedom to use different plant genetics and to apply the most effective LEDs.
“Over the years, we have continuously merged the best options provided by the LED world with smart optical concepts and consider the peculiarities of the various cannabis genetics out there. The result is a ground-breaking line up of illumination gear, for efficient cannabis production along with a research and development team who strive to optimise the next product generation working today also beyond illumination,” says Christian Hochfilzer, Director of Horticulture at SANlight Solution.
Holistic optimisation of raw materials and production processes beyond the illumination gear
Keep in mind that the focus is on the crop and illumination whereas the design of the light source is a consequence borne out of this approach. Hence, we have decided to use the term illumination gear rather than light source or luminaire for our product line-up. SANlight presents two major product families the FLEX-Series and the Q-Series. The bars of the FLEX-Series are sought-after for their use in multilayer production facilities, where homogeneous light distribution at close proximity is promoted to ensure a healthy and concise growth process.
The optimal ratio of bar-spacing and distance to the crop canopy is simulated and custom tailored to the specific requirements of the production facility. The specifically shaped optical system creates a vertically extended and well illuminated cross section for the young crop. The name of this product family – FLEX-series – stands for the ease in project planning and execution. The illumination gear is widely used in the production of cuttings and seedlings.
The Q-Series is specially designed to illuminate larger plants as they are common in the vegetative and generative phase of cannabis production. The free-form optics in front of each LED-emitter provides a square like, batwing radiation. What is the advantage of this unique design? The light is evenly distributed onto the canopy area underneath the illumination gear. The optically directed light rays of the Q-Series emulate the natural light coming from the sun on a partly cloudy sky, penetrating all the way down – deep into the plant canopy. This is true illumination.
Where is the future? In solid-state light sources
Why for anyone’s sake should one invest in a solid-state lighting solution rather than in a cheaper(?) conventional HPS light? The simple answer: considering the total cost of ownership it pays off. In the countless installations we have established all over Europe we have one piece of consistent feedback; you save energy as the light generation is more efficient, the light distribution towards the canopy of the crop is more efficient, the heat radiation towards the plant is reduced and the thermal losses in a glasshouse or indoor facility are reduced and help to save investment and energy costs on the HAVC system.
Another fact is, that the optimised spectral emission of LED light sources results in a higher relative concentration of cannabinoids, cannabidiol or terpenes. But the best thing is that our illumination gear is a truly forward-looking investment. We support research programs to breed more resilient cannabis genetics that grow perfectly under dedicated emission spectra. We are perfectly aware that the spectral composition of today might be disused in the future. We have already designed our Q-series in such a way that one can easily replace the LED top part with the latest generation available. No need to replace the illumination gear, simply exchange the LED topping.
What is smart? Cultivating outdoor, in a greenhouse or in an indoor farm?
The answer is simple – all three methods do make perfect sense on their own. Looking at the Swiss market for example, the cultivation of CBD cannabis on open fields was largely expanded in the season of 2019 for the simple reason that the money is in the extraction of CBD oil, and product derivatives and the consistent quality of the plants and buds is not critical for success. What counts is the availability of a large volume of finely chopped plants including the buds for extraction. There is one grow cycle per year. SANlight supports this production approach with FLEX-PRO-Series for seedling and/or cutting nurseries and the Q-Series for young plant propagation in greenhouses during spring and early summer. More advanced is the production process in greenhouses that can be shaded easily to control long day and shorter day cultivation. These facilities allow four and more grow cycles per year.
Official approval from the authorities provided – some producers even grow THC strains in greenhouses with appropriate security protection. We often see that existing greenhouses (e.g. former tomato production sites) are refurbished and converted into cannabis production facilities. The products delivered are predominantly dried buds and chopped plants both well separated. A controlled illumination solution is required for the vegetative and generative phase working as so-called supplemental light. The illumination period is usually set to 18hrs per day for the vegetative phase and to 12hrs per day for the generative phase. Whatever is available as natural daylight is taken in the production. The Q-Series is used here as supplemental illumination and the light intensity is adjusted by a control system relative to the available daylight depending on the production phase, weather condition and yearly season.
Further down this article we will show in one of our best practice reports what challenges a greenhouse grower faces. And finally, the indoor production facilities where the plants are only illuminated with artificial light under a fully controlled grow environment. The reproducibility and also the productivity of the grow process can further be increased, and we see often five and more production cycles a year with consistent product quality. The footprint of these facilities has also changed over time. Earlier this year we started the roll-out of fourth generation indoor facilities in Europe.
What can we prove?
Case studies
Let us start with a greenhouse facility which has been in operation for more than three years. Naturally, it took some time to optimise the various production parameters mentioned earlier. After one and a half years in operation we teamed up with the producer and his customer to track the influence of the ambient conditions outside the greenhouse and the seasonal changes of the daylight on the product quality and yield. The facility is used for THC production. In this study we measured the relative THC and THC-acid content of the bud, the weight of the dried buds, the THC yield per plant in gram over a period of 12months or four grow-cycles. We could clearly demonstrate a considerable yield variation depending on the position of the plant in the greenhouse. Furthermore, it was shown that there is severe yield variation between the four production cycles. One negative variable is the high temperature during summertime although there is enough natural daylight.
Interestingly, the highest yield was achieved in the autumn/ winter production cycles. In addition, we have also compared the results using supplemental illumination with full-spectrum LEDs and HPS at the same electrical power consumption per square metre. With a year-round average yield increase of 45%, the full-spectrum LEDs were outperforming HPS by far. The yield gap is larger during the lighting season (October – March) and narrows down in the summer months. In conclusion we were able to show a cost advantage for full-spectrum LED-illumination in a greenhouse facility. To bring the production variation and losses during summertime further down we have thought up ideas to improve the HAVC system and shading concept in the greenhouse. But it became also clear, that it is not cost effective to lay out the facility for worst case climate situations so there remains the risk of yield loss due to weather extremes.
These are the limiting factors for a greenhouse facility. In further studies we have started to look at indoor facilities in more detail. As mentioned earlier in this article we have had some customer feedback about indoor farms where there have been grown various types of crops outside the cannabis world. In one of our home markets we have worked together with cannabis pioneers to optimise professional indoor farms for CBD cannabis, and today we are shipping fourth generation facilities. They work under CO2 enriched closed environments in an air-tight cabin where the HVAC and watering system is completely controlled and decoupled from the ambient. The production is in moveable two storey racks and facilitates running five or more production cycles per year. The reproducibility and yield of the production process is excellent, and the high-grade dried buds are used for premium medical or recreational products.
Based on our experience with smart and integrated illumination solutions for greenhouse and indoor farming we strive for further improvements in product quality and production yield by combining new plant breeding programs with innovative illumination concepts. Focusing on cannabis production and driving the process improvement together with our customers puts SANlight Solution GmbH as an engineering partner and equipment supplier at the forefront of an emerging phytopharmaceutical cannabis industry.
Christian Hochfilzer
Co-Founder
SANlight Solution GmbH
+43 650 8421158 (Office)
christian.hochfilzer@sanlight-solution.com
https://www.sanlight-solution.com
This article has also appeared in Health Europa Quarterly Issue 11, which is available to read now.