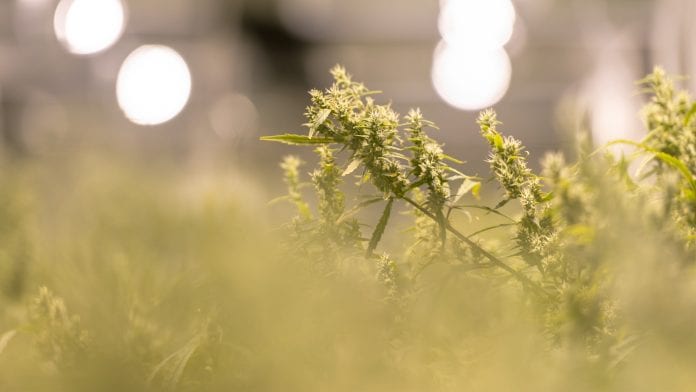
Despite widespread reform in Canada challenges still exist which must be overcome – including cannabis quality.
In cannabis, there are very few topics so polarising and is of such public interest that political parties mandated its presence onto their party platforms; so broadly impactful that it is now virtually impossible to separate the medical cannabis from the recreational in isolation of the end user.
Canada is now regarded as a world leader, being the largest country to federally legalise both recreational and medical use, with a deeply regulated process for licensing production facilities and providing a set of standards that other countries are examining, for better or worse, as each determines their own evolving position on this miraculous plant.
That being said, it is no secret that a growing swell of public and professional opinion is that the supply of product is of notably poor cannabis quality, even astonishingly so.1
There are several potential contributors to this state of affairs, and when distilled down to the root causes, the most profound issues stem from market demand, investment landscape, and facility design.
When the United States lifted prohibition of alcohol in 1933, it released a 13 year drag on an industry that had hidden its true level of demand in bootlegging, speakeasies, hoarding, and even the prescription of medical liquor.
The cannabis sector has suffered a longer cultural and legal prohibition, however, the attention and fundamentals in the cannabis sector remain. There was, and remains, a clearly articulated and significant amount of pent up demand, with healthy margins available, and a limited amount of supply on the market. A perfect recipe for profit, which laziness has turned sour.
Cannabis quality
Companies which may have started with all the best of intentions, found that multi-million dollar ‘clean room’ construction projects were harder to manage and deliver than they expected. Case in point: in the early (and not so early days) at one of the earliest and largest Canadian licensed producers, electrical and mechanical contractors were instructed to set up equipment one way, then remove it and install it a second way, only to be again instructed to reinstall the same equipment a third way. Frustrated, perhaps, but still billing by the hour.
Crop failures abound, but so long as mouldy product was irradiated to kill the mould spores, the product could pass the testing with Health Canada’s blessing. Yes, this irradiation process rendered the cannabis flower brittle, and, to a connoisseur, greatly impacted its terpene profile and visual appeal. However, supply and demand being what it was, that flower could still be sold and at a profit.
If substandard flower can still be sold, why bother trying too hard? If the poorest quality product can still be processed, converted to oil and sold at a profit, then any effort into quality is wasted, is it not?
Thus, by hook or by crook, the market became flooded with the most quickly produced flower, knowing that even the poor quality product could command a price.
Investment
As far as the investment landscape, anyone who has raised significant funds for a startup knows the challenges involved with establishing a defensible value for the company while allowing the investor sufficient room to grow their investment capital to provide a healthy enough return to justify the investment in the first place.
This tug of war between investor and company is made more pronounced with early capitally intensive startups – ones that require significant funds up front to be used to build up infrastructure and services before products can be produced and thus, revenue generated. Sound familiar?
Software startups often have a small round of friends and family investments that allow the development of a ‘proof of concept,’ or minimal viable product to be developed. Something that can be taken to market and sold, allowing for testing of valuable features which may pique the interest of customers, even ensuring some room to pivot away from a set of features that is of little interest and exploring ones that unexpectedly become more popular.
Thus, the business rides a wave of demonstrated success before it requires additional investment capital, leap frogging increases in value which are justified by the increasing revenue, user base or popularity of the application.
The green rush
It is no secret that when the Canadian federal government unveiled its legal licensing structure, the Canadian cannabis sector became the next gold rush overnight – the green rush was born.
Hundreds of millions of dollars were invested broadly. Billions of enterprise value was created. People became wealthy. Poor planning, inadequate thought, and insufficient resourcing of all kinds shattered the dreams of wealth of many. A general lack of business maturity caused many to ante into a game they were unprepared to properly play.
Under Canada’s current regime, cannabis production requires some large amounts of hard renovation and construction, uses expensive equipment, and needs complex engineering drawings for permits and approvals. While scaling of business and production capacity is possible, the steps between expansions are sizeable, and render a cost effective cannabis production ‘proof of concept’ impossible.
This results in fundamental challenges in attracting investment capital, punishing creativity and rewarding lowest-cost construction designs and plans. Large rooms with as few walls as possible have become the de facto standard, leading to unforeseen exposed risks as these larger rooms became susceptible to widespread contamination, plant based disease outbreaks and a constant struggle to maintain the precise lighting, temperature, and humidity conditions for all plants within the space.
You quite literally get what you pay for
At the head of the line for a fundamental industry evolution is the most difficult adaptation – design. Easiest to change at the beginning before problems have occurred and before wisdom whispers its warning.
A company whose only focus is on production capacity may simply not pay attention to the flow of staff in and out of the production areas. Therefore, staff working in one area may bring contamination to another area simply due to their path of travel, over which they have no choice. Knocking down walls and rebuilding rooms is not feasible after cannabis production begins.
As issues in production may not become apparent for several harvests, fault may be levied to individuals or cannabis quality control processes when the true root cause lies fundamentally elsewhere. The legal cannabis sector simply isn’t mature enough to have hardened enterprise root cause analysis processes adapted to suit their purposes. The current sentiment is ‘build more, grow more’ – quite literally rinse and repeat.
What is worse is that design is so fundamental that, once rooms are built and hallways connect from space to space, it is financially impractical to decide after the fact that the hallways need to be widened to allow for Good Manufacturing Processes (GMP) to be established. Moving walls impacting production spaces would contaminate or cripple any existing harvests and delaying the next growth cycle for a two to three month construction window becomes too significant a hit to revenue to tolerate.
Even more profound is, when combined with the cost controlled construction and an ever present pressure for more supply more quickly, the facility design impacts the ability to adequately control the growing conditions of the plants and becomes an unrecoverable error. A small handful of Canadian producers have found a way of bucking the trend and have a design that supports a different outcome, and with the rampant competition and inevitable commoditisation in the future, there is little incentive to help out a rival and guide them on just what they’re doing wrong. Rather, accept their impending failure.
That large 2,500 square metre room, once the apple of the CEO’s eye, becomes a constant reminder of the challenge of controlling airflow across so broad a space, restricting the spread of mould, mildew, and cross-contamination, and avoiding damaging the vegetating cannabis plants in row one while the flowering plants in row two are harvested. In short, a production nightmare with a cost to resolve that is simply too high.
While the market tolerated this paucity of cannabis quality for a short while, the black market has continued thriving. One of the primary drivers behind the evolving legislative landscape was controlling and limiting the underground cannabis railroad. The most recent research from New Frontier Data reports that 80% of cannabis sold in Canada is still coming through the black market.2
Inevitably, the problem with rushing is a lack of preparation. Rushing to market exposes poor planning and execution, resulting in poor quality production. Proper preparation, with educated investors who ‘get the programme,’ and a well-designed facility plan that takes quality control processes into full consideration can provide the holy grail in this industry; consistent cannabis quality, repeatable conditions harvest over harvest, and enough capacity to handle the loud wholesale demand for quality cannabis flower.
Canada’s cannabis quality problem has a solution. It just takes a little more patience and critical thinking to get there.
References
1 https://420intel.com/articles/2019/12/02/poor-quality-cannabis-root-canadas-woes
2 https://www.bnnbloomberg.ca/cannabis-canada-daily-black-market-accounts-for-nearly-80-of-pot-spending-1.1222534
James Mackenzie
Nordik Leaf
+1 6132405141
james@nordikleaf.com
nordikleaf.com/a/pre-launch
This article appeared in the first issue of Medical Cannabis Network which was out in January. Click here to subscribe.