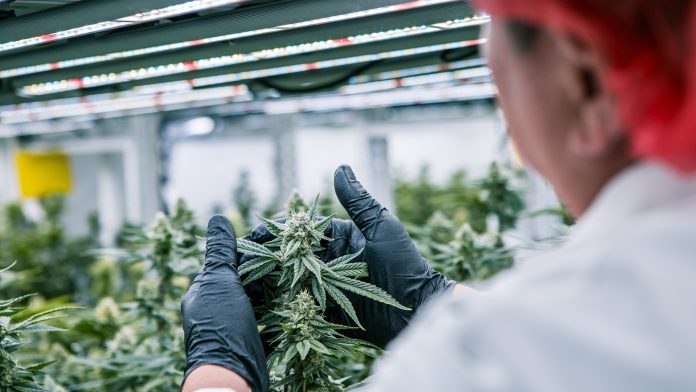
Timo Bongartz, general manager, EMEA, Fluence discusses how LED technology could benefit recreational cannabis cultivation in Germany.
Green is the new gold. Four hundred tonnes of it, in fact. That’s how much annual demand there could be for cannabis in Germany, according to a November 2021 report from economist Justus Haucap. When recreational cannabis is legalised—a seeming inevitability at this point under the coalition government’s October 2021 contract proposal—it will bring an estimated 27,000 jobs and €5 billion in annual tax revenue.
It will also create perhaps the most competitive cannabis market in the world.
German recreational cannabis cultivators
German cultivators—and others who will produce cannabis for the German market—won’t have the luxury of building an operation by trial and error over years—as many other markets have done—lest they risk falling well behind the competitive curve in consistently growing high-quality recreational cannabis. It will be a mad dash to the finish line to meet massive demand. Those who get off to a great start may well be the ones who dominate the cannabis landscape in Germany for years to come.
The question, of course, becomes: How do cultivators do that?
The answer—and one of the critical underlying benefits to German cannabis operations—is to rely on the proven practices and technologies that other, more well-known markets have established in their own countries. Combined with a bit of classic German ingenuity, the stage is set for Germany to become a global leader in recreational cannabis production.
The same is true of cannabis. The precedent, in many respects, is the United States, a collection of more established markets that have effectively laid the groundwork for continued innovation and iteration.
There are a few critical lessons from those markets that German operations will be wise to adopt from the beginning—lessons that may seem obvious now, but which were hard-earned in the States and elsewhere.
Controlled environments are the only profitable way forward
First, controlled environments are the future of not just cannabis, but commercial food production as well. In a hypercompetitive market that will come to dominate German cannabis, the vast array of suppliers and cultivators will mean a near-infinite number of options from which consumers and distributors can choose. Low-quality, high-volume models that rely on outdoor production will not satisfy the market—especially the medical cannabis market. The opposite is also true: Low-volume, high-quality products will not be profitable for most operations. The natural solution, then, is to adopt a business model that can consistently deliver quality products year-round at high volume.
Controlled environments are quite simply the only way to do that. With this model as the starting point, cultivators can then begin to assess and establish their business goals and forecast expenses. Some cultivators may lean into flower-heavy production. Others might emphasise cost-efficiencies to lower product price points, while still others may have a model centralised on extracts and edibles. Each comes with its own set of unique challenges—labour costs, facility size, allocation of growing vs. processing space, varying capital expenditures, and plant genetics, to name a few. It can sometimes be an overwhelming exercise, which is why it’s critical that every operation not only invests the time to do it early in their life but also pinpoint the exact customer benefits they aim to provide and the needs they hope to fulfil. Doing so will help orient the business, define the criteria to meet its bottom line and establish the criteria to evaluate and dictate every future decision.
Deploying the right technology early
Once recreational cannabis cultivators decide to adopt a controlled environment production model, the natural—and by far the most important consideration—will be the capital investments in lighting fixtures. Everything else that happens in a controlled environment is largely based on that choice.
Future market leaders and laggers are decided in this phase. Indeed, making the right decision on lighting early may be the single greatest factor in determining which operations can get to market in those first few harvests, and which are plagued by low quality or inconsistent production timelines.
Fortunately, other markets have done much of the leg work. A decade ago, when cannabis began its entry into individual states in the US, high-pressure sodium fixtures were the industry standard. LEDs were simply not cost-effective enough to justify the enormous initial capital expense. As years passed and LEDs grew cheaper, their benefits became more widely known and their initial cost was less of an issue. To remain competitive, many cultivators were forced to retrofit their facilities with LEDs to meet the growing demand for year-round, high-quality products, a trend that continues in those markets today.
German operations shouldn’t have that problem. They can easily adopt proven LED lighting solutions to meet demand, hit top-line performance goals and capture every euro of revenue there for the taking.
Capitalising on industry-leading benefits of LEDs
LED-based controlled environment models aren’t without complexity. The ability to control every factor within an environment means that cultivators must control those factors with total precision and an exceptional understanding of how to maximise every plant’s potential. The effectiveness of the tool being used means little if the person wielding it isn’t equally effective.
There are myriad controls for which cultivators must account when using advanced lighting products and strategies—vapour pressure deficit, humidity, CO2 saturation, temperature setpoints, daily light integrals, pest control and many more.
Again, the number of considerations can skyrocket quickly, making it all the more important that recreational cannabis cultivators can fall back on the two most important factors that dictate long-term market success: quality and consistency, both in yield and cycle times.
In years past, those two goals were often mutually exclusive. A focus on one would limit the other. LEDs have made that dilemma extinct.
Achieving best-in-class quality and consistency
Fluence’s research is pushing the boundaries of cannabis production models and setting new standards and practices for cultivators in the process. Together with leading partners like Wageningen University & Research (WUR) and U.S.-based medical cannabis provider Texas Original Compassionate Cultivation (TXOG), we set out to answer two of the most pressing questions about LED-based lighting strategies: “What type of spectrum should I be using?” and “How much light should I be delivering to my cannabis plants?”
While every cannabis cultivar will respond differently to its environment, our research has clearly shown the performance benefits of adopting broad-spectrum lighting at high intensities.
Researchers in our study with Texas Original Compassionate Cultivation analysed Type I, Type II and Type III cannabis response to broad-spectrum lighting using various percentages of red light under high PPFD. In each case, broad-spectrum with lower quantities of red light generated the driest weight per plant. In Type I cannabis, a balanced spectrum of white light generated 17% higher yields than the next highest-yielding spectral solution, which contained a larger concentration of red light. Cannabis grown under the more balanced spectrum also significantly improved morphology. Plants grown under a balanced white light spectrum were also free of photobleaching in their upper buds, a development that typically occurs in plants grown with a higher fraction of red light.
In the WUR study, researchers found that in some cultivars, monoterpene and cannabinoid content, including THC, CBD and CBG, is significantly inversely proportional to the fraction of red light in the production spectrum. With these cultivars, the more balanced white light spectrum induced a 20% increase in cannabinoid compounds compared to spectra with red light ratios as high as 90% or more. In other words, more red light equals fewer desirable traits.
These performance increases are quite significant, especially for operations competing in crowded markets that need to meet high demand with superior quality.
Our research similarly shows that achieving those benefits relies heavily on the number of light cultivators deliver to their plants. The TXOG study found that the largest yield increase occurred between 1,100 and 1,500 µmol/m2/s. A 26% increase in light intensity increased yields by 27% t. Yield continued to climb even toward 2,100 µmol/m2/s where researchers observed a yield peak. Environmental parameters were closely monitored throughout the experiment. Researchers noticed that under treatments exceeding 1,500 µmol/m2/s the management of these parameters becomes far more challenging.
Once recreational cannabis cultivators realise LEDs’ superior benefits not just to energy efficiency but to operational performance, the desire to achieve that success again and again and again becomes the standard for production moving forward. Luckily, because they’ve already decided to invest in LED-based controlled environments, finding such consistency becomes a matter of adjusting to seasonal differences in lighting and perfecting minor variations from harvest to harvest.
The approach becomes three-fold. Use existing, proven research to form a baseline for cultivation methodologies and best practices. Lean on partners—like Fluence’s horticulture services team that puts local experts on the ground with cultivators—to apply that research and their own domain expertise to solve an operation’s unique cultivation challenges. Deploy the lighting and cultivation strategy that achieves stated business goals and delivers tangible results for customers.
Now that’s German precision engineering.
About Timo Bongartz
Timo has spent more than a decade helping businesses to innovate their business models and starting new ventures. His passion for accelerating business transformation—combined with a childhood affinity for cultivation—ultimately led him to the horticulture industry. Today, Timo serves as the general manager for Fluence‘s EMEA region, empowering food, ornamental and cannabis growers across Europe, the Middle East and Africa to achieve their cultivation goals through advanced horticultural lighting technologies. Together with his interdisciplinary, multi-national team he supports greenhouse growers and vertical farmers in over 20 countries and manages industry leading photobiology research.
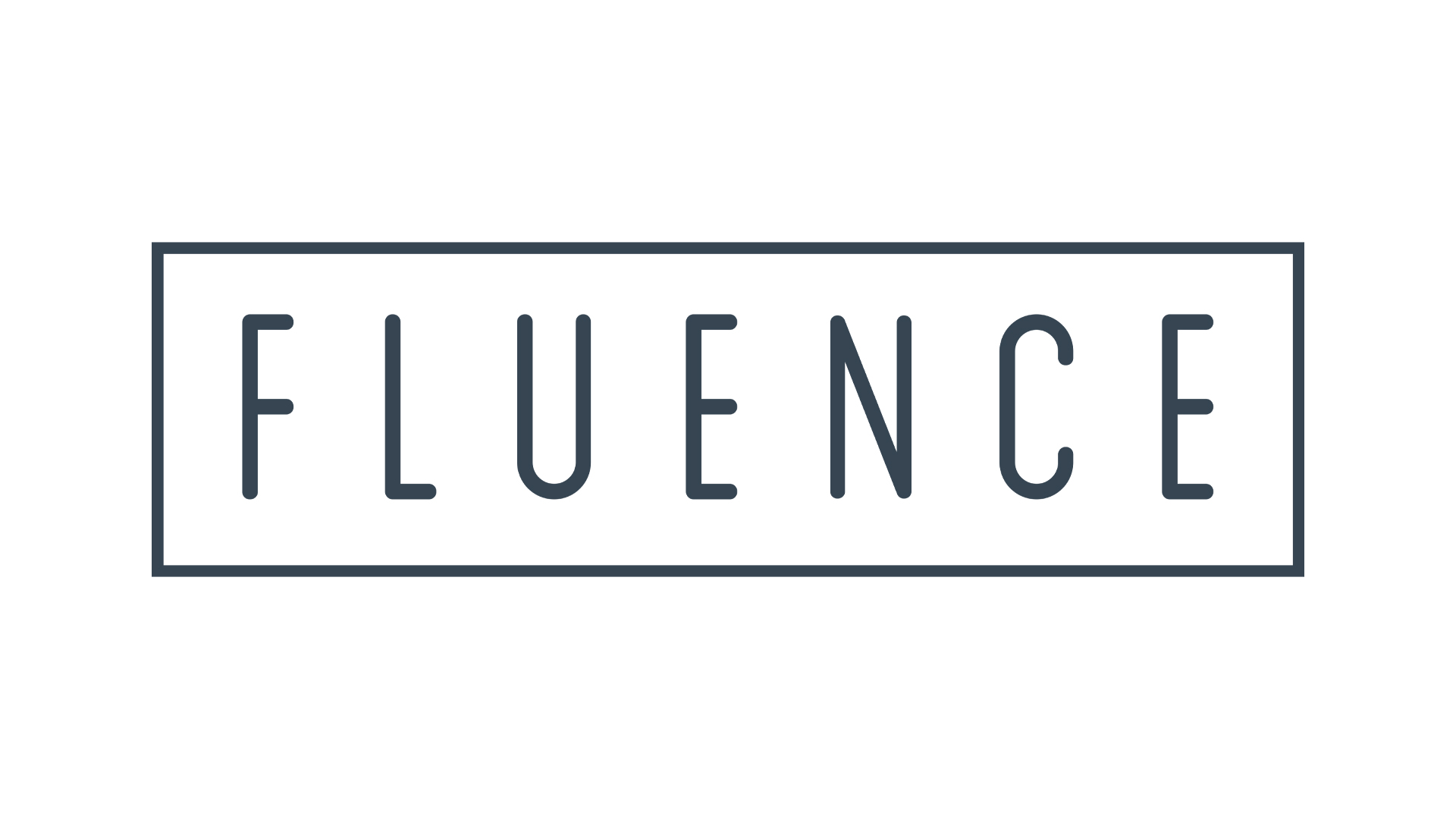