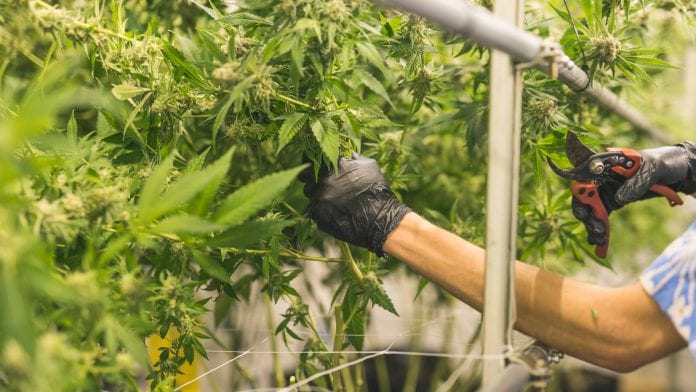
Grow2Guys offers lessons from North America for European indoor cultivation facilities.
Grow2Guys, a division of urban-gro, Inc, has provided full-service mechanical, electrical, and plumbing (MEP) engineering services for commercial owners since 1982. The firm’s portfolio includes more than 300 cannabis-related projects, including new construction and renovations to indoor cultivation facilities and greenhouses. With the rapid advancement of technology in a strict regulatory environment, we have learned valuable lessons about cannabis cultivation.
MEP engineering and design considerations for cultivation facilities
As part of the design process, urban-gro must first understand the required design standards that must be met. For European markets, cultivation facilities must be Good Manufacturing Practice (GMP) certified. Specifically, our scoping process for cultivation facilities focuses on the area of the cultivation room and total square footage. Once completed, we then look at the total canopy area and number of plants in the room. It is essential to understand the watering rate per plant to estimate the transpiration load which informs the design of the environmental control system. Whether your cultivation facilities uses emitters, hand watering, ebb and flow, or hydroponics, the watering approach is crucial to calculating waste – not just through evapotranspiration, but also evaporation in soil and within beds.
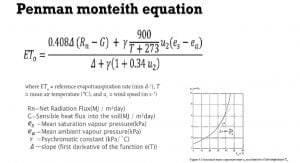
The type of media is also essential, as is the number of lights in the room. Both add to the sensible load that contributes to our calculations in designing the environmental control package and sizing equipment. For example, the heat released by each light fixture needs to be accounted for in the water distribution schedule. Given the number of factors at play, it becomes complicated to accurately calculate the sensible load collection and size equipment appropriately.
The circulation of air using fans is another important consideration. Fan velocity and power; number of fans; and placement will all affect the overall cultivation environment. Temperature set points such as lights on and lights off are an essential parameter in determining equipment sizing and calculating the environmental control systems.
The design team must understand the plant
Transpiration is key to proper ventilation
The Penman-Monteith equation calculates the total watts in the room, taking into account secondary fans, lighting, exterior factors, canopy size, and estimated water transpiration per plant. With this information, we can gauge how cultivators are watering, ensuring that we are not overwatering or underwatering plants.
Variables in the flowering room
There are four main variables in a flower room that affect plant growth:
- Water and nutrients;
- Lighting;
- CO2 levels; and
- Environmental control.
The water and nutrients, lighting, and CO2 are typically standardised fixed variables outside of some slight variances. The most significant variable is the environmental control system. Without proper design, the environmental control system is the most influential variable in terms of temperature and relative humidity control within a cultivation space. With properly designed equipment, the environmental controls variable becomes less volatile, enabling efficient growing and indoor cultivation.
Unfortunately, environmental control systems are commonly the first to be value engineered (VE) out of a project to cut costs. When value engineering equipment, specifically environmental controls equipment, standard air conditioning is often used as a replacement. Because standard air conditioning is not designed for cultivation environments it has been our experience that this option leads to increased pest pressures and reduced yields.
Understand the plant and VPD
Vapour Pressure Deficit (VPD) measurements are an indicator which can help identify the potential for plant transpiration. Controlling the VPD can maximise transpiration, which in turn, maximises the plants’ nutrient uptake and yields bigger, healthier plants. VPD is a single indicator that considers the room’s environmental conditions at certain times during the growing process. Early, middle, and late stage cultivation can have varying VPD control or set points.
VPD is one method of approximating water stress on a plant. Operational and economic factors related to VPD are also important considerations. For instance, if you control a room at 80°F with 60% relative humidity (RH), that may be an ideal VPD set point of 1.5 kPa, but would create an environment more conducive to pest propagation, increasing the likelihood of pests like spider mites or aphids. Conversely, if the same room were controlled to 70°F and 40% RH, the ideal VPD of 1.5 kPa would not be realised. The difference between these two environments is that the cost of the mechanical equipment required in the second room is 50% higher because of the lower RH set-point. The relationship between VPD, room set points, and equipment cost is typically exponential. The room operating at 80°F and 60% RH will incur substantially less mechanical equipment costs, but may have other issues. The solution is to find a set point where the mechanical equipment operates at its highest efficiency, while maintaining the proper VPD and environmental control.
Stay in the range of VPD
Vapour pressure is created when a plant attempts to transpire. The pressure against the stomata on the plant provided by the atmosphere is what allows for transpiration. Therefore, if there is too much pressure, the plant will not transpire; this will result in powdery mildew and mould issues. Too little pressure, meanwhile, will cause the plant to over-transpire, which produces very unhealthy plants and lower yields.
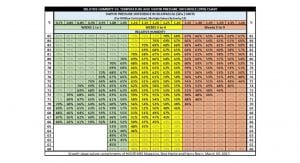
Choose the environmental controls which support your production goals
Do not move in the wrong direction
The goal is to maintain stable relative humidity and temperature with integrated equipment, as opposed to fluctuating values which occur because of standard air conditioning, standalone dehumidifiers, and other equipment which are not controlled holistically. Conventional air conditioning delivers variance in temperature and relative humidity, particularly as lights cycle on and off. Although humans may not be able to feel or experience these incremental fluctuations, plants do.
Select for efficiency and purpose
There are several environmental control options to consider when it comes to optimising system efficiency.
The first option is the chilled water approach. Although very popular, it is the least efficient way to control dehumidification. It has the highest capital expenditure, lower evaporator (cooling coil) temperatures, and a separate system for reheating. The equipment is not truly redundant, even though you may have a redundant fan / compressor, chiller, and pump. It is also expensive to operate and relatively inefficient.
The second option is the standard direct expansion (DX) air conditioning. It has a higher evaporator temperature, higher nominal tonnage to meet the latent load; and no dehumidifiers, which makes it insufficient to reheat. Paired with ongoing challenges around control and environmental stability, this option is also inefficient.
The third option would be customised DX cultivation units. These have lower evaporator temperatures and constant volume fans. These tools make it more efficient than chilled water and standard DX air conditioning units.
The final option is perhaps the best and most efficient. Purpose-built DX cultivation units have extremely low evaporator temperatures, modulating compressors, modulating evaporator fans, modulating compressor fans, and meet the moisture removal requirements with smaller nominal capacity.
Studies results on the comparisons between environmental controls systems are persuasive. In side-by-side room comparisons, the use of customised or purpose-built equipment increased the net yields by 20% – 30% with no losses due to microbial contamination.

Choose the correct HVAC environmental control equipment for the purpose
Ultimately, the right heating, ventilation, and air conditioning (HVAC) environmental control equipment will provide a more stable environment, maximise plant health and yields, minimise crop loss, minimise utility costs, save on capital expenditure; and maximise sustainability. Operating in these design conditions, DX is the best solution for environmental control relative to the more inefficient system alternatives. Without proper control, the environment may become too hot or too cold, exponentially compounding the cost of cultivation.
Tips for the design and build of European high-performance cultivation
MEP personnel should review property infrastructure and project details
Other factors to consider before designing a facility, whether it is new construction or an existing structure undergoing redevelopment, is the property infrastructure. Communicate with your architects and structural engineers to ensure that they understand the design requirements of cultivation facilities and the unique considerations specific to the local climate (cold, warm, humid, dry, etc).
Another infrastructure factor to consider is that cultivation equipment tends to weigh more than standard air conditioning. The weight must be taken into consideration as it relates to structural load capacities to ensure the building will support the equipment. These infrastructure factors differ depending on whether the facility is existing, new construction, or a pre-engineered steel building.
Finally, be mindful that interior finishes like paint and epoxies will off-gas as they cure, which may affect plant health.
Phased construction can support the project budget
A smaller, well-built facility is better than a larger, poorly built one. Instead of focusing on maximising canopy size, consider the budget and invest in a well thought out facility, equipped with the right environmental controls. We advise that cultivators focus budgets on the right environmental control for each type of cultivation room: veg, flower, and mother clones. By investing in mechanical equipment over canopy, you will see a much quicker return on your investment, ensuring successful harvest of each plant and the passing of regulatory inspections. Construction phasing can be useful for meeting budgets, timelines, and managing cash flow while assessing demand and refining internal processes.
Design today for tomorrow’s market
Across North America, urban-gro has seen the wholesale prices drop from $2,600/lb (2014 prices in Colorado) to $800/lb in 2020. To compete successfully in this evolving market, it is imperative to invest in sustainability, equipment efficiency, and reduction of operating expenses. These goals are achieved by using purpose-built equipment, as opposed to conventional systems designed for other commercial environments.
Do not make rash decisions by focusing solely on speed to market. A rushed approach may result in incorrectly designed and inefficient systems to dehumidify your cultivation rooms. By working with experienced engineers in the design of indoor cannabis cultivation, you will avoid the short term impacts of design and construction coordination and delays, as well as the longer term, more financially consequential issues of lower yields and lower quality yields.

Brian Zimmerman, PE
Grow2Guys, a division of urban-gro, Inc
brian.zimmerman@grow2guys.com
This article is for issue 3 of Medical Cannabis Network. Click here to get your free subscription today.