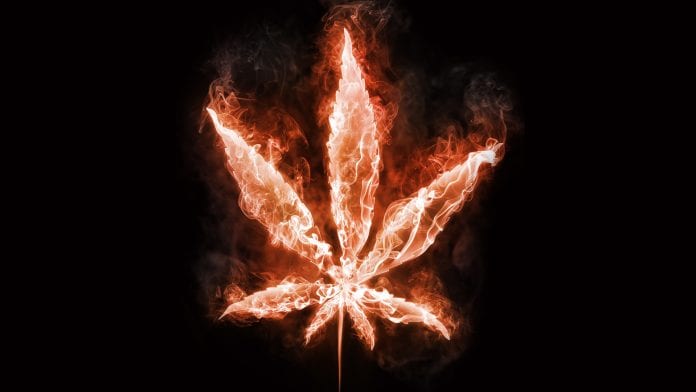
HAL Extraction Technology Ltd. builds hazardous location oil extraction facilities to keep people safe – how can you apply this to cannabis extraction safety?
Before recreational cannabis was first legalised in the USA, and anyone even thought about cannabis extraction safety, butane honey oil (BHO) was the leading choice for consumers. Unfortunately, the chemical process used to extract the oil from plants was breathtakingly dangerous. ‘Open blasting’ was the technique used in the black market and by dispensaries making oil for medical marijuana sales. Of course, the operators were enveloped in a cloud of flammable butane. Colorado firefighters were called to about 40 fires and explosions caused by open blasting in the first three months of 2014. The actual number of fires was far higher, as operators were disincentivised from reporting their burnt wall, or small burn on a hand.
At the end of 2013, the State of Colorado began the process of developing regulations for a cannabis market. They had to start from scratch; there were no existing regulations to use as a model or guide. An early release of regulations banned open blasting. Extraction equipment was now required to be ‘closed-loop’ to ensure that solvent was captured for reuse rather than released to the atmosphere. Equipment also had to be certified by a ‘nationally recognised testing laboratory’ or receive a ‘peer review’ by a professional engineer (PE). In addition, facilities that were used for extraction had to be inspected and evaluated by a certified industrial hygienist (CIH – occupational hygiene or environmental health and safety specialist) or a PE prior to operation.
The origins of HAL
Linn Havelick, a Colorado CIH, retired in 2014 and decided to look at consulting in the newly growing cannabis industry. Of course, cannabis was still illegal at the national level, and it was possible that his certification was at risk working with an illegal industry. The complete lack of occupational health and safety, chemical process safety, or engineering expertise in the newly legalising field meant that there was a great deal of room for significant contributions. Havelick decided to consult in the field – if the American Board of Industrial Hygiene wanted to challenge his certification then that was a risk he was willing to take due to his impending retirement.
The initial regulations, effective from July of 2014, resulted in a steep reduction in fires and incidents, but not elimination. Fires and injuries continued, albeit at a much lower rate. However, the new and rapidly evolving industry was struggling with the high cost of designing and constructing hazardous location rated facilities. An open blasting setup was orders of magnitude less expensive than a facility that required specialised engineering design, specialty electrical components, sensors, explosion proof rated fans and motors, and more.
Havelick realised that any facilities that used flammable solvents for extraction would eventually need to abide by local, state, national, and international building and fire codes. At the beginning of 2016 he formulated the concept for a relatively inexpensive approach to constructing these types of facilities. Based on these ideas, Havelick formed HAL Extraction Technology Inc. (HAL) and filed a patent application for a ‘closed oil extraction booth with integrated ventilation system.’ He hired several engineers and began work on initial prototypes; the first booth sales were made in January 2017. The patent was granted effective March 19, 2019. A bonus for HAL was that the extraction booth could be used for a variety of hazardous solvent applications such as distillation, hazardous materials storage, and essential oils extraction.
The regulatory environment for HAL’s extraction booths was remarkably complex. The booths were subject to existing codes related to electrical, hazardous locations, exhaust ventilation, steel thickness, building interior layout, hazardous materials quantities, sensor function, control panel construction, and more. In addition, many product fabrication standards could apply. Then, in the USA alone, there were at least several thousand jurisdictions to which these requirements could apply, each with their own interpretations.
On top of that complexity, the fire marshals and code officials were quite aware of the history of fires and explosions related to open blasting. Often not understanding the difference between newer equipment and open blasting, and not being familiar with plant oil extraction, the officials go over building permit applications for this equipment in excruciating detail.
Beginning with a safety background supplemented with talented engineering, the extraction booth documentation was submitted to Underwriters Laboratories (UL), the preeminent standard setting and testing organisation in North America. Prior to working with HAL, UL declined to work with industries related to the marijuana industry; the plant was still illegal at a federal level. In 2018, UL developed the first draft standards for plant oil extraction equipment, including plant oil extraction booths and pods plus butane and propane solvent extraction equipment.
In 2019, HAL’s booths became the first equipment certified under UL 1389, Outline of Investigation for Plant Oil Extraction Equipment. When North American jurisdictions see the UL mark on HAL’s equipment, that is often all the review they need to be comfortable that it is the best in the market.
Equipment listing by nationally recognised testing laboratories such as UL, Intertek (ETL) in North America and CE in Europe help local officials determine that the equipment has met all applicable standards. For instance, nearly every electrical building component you will see will carry one of these marks. Many jurisdictions will not allow electrical building components to be used within their borders unless they carry the appropriate mark. HAL is working to add UL-Canada, CE, and EXP certification marks to its equipment soon.
Working with volatile solvents can be extremely dangerous, or it can be as safe as working with other chemical processes. Keeping people safe when working with solvents such as ethanol, butane, hexane, pentane or propane involves at least seven layers of safety.
HAL extraction booth: seven layers of safety
Layer one: training
Without a solid understanding of the chemistry and physics of the processes being used, an extraction technician is automatically risking tragedy. For example, in March 2016 two technicians in a New Mexico dispensary laboratory working with a closed loop butane extractor had an accident that resulted in life threatening burns over much of their bodies. While many safety related problems can be identified in that incident, any training that included concepts as simple as keeping flammable solvents away from sources of ignition could have prevented the tragedy.
Layer two: ventilation
Work areas where flammable solvents are used must be ventilated to prevent the accumulation of vapours. If vapours are kept to concentrations below the minimum required to ignite (lower explosive limit), it is difficult to get a fire started. Of course, exhaust ventilation must be sent outside the building to prevent indoor accumulation of vapours.
Layer three: eliminate ignition sources
Flammable vapour can be ignited by sources such as heating elements, fans, motors, open flames, metal cutting, electrical connections, or static electricity. Ignition sources are kept out of the extraction work area, or inside electrical equipment designed to contain an ignition event (explosion proof or EXP). By eliminating ignition sources, even if ventilation and training fail, vapours will not ignite.
Layer four: explosive vapour monitoring
Butane and propane solvent vapours can reach to above the lower explosive limit (LEL) before the human nose can detect them. Extraction facilities using flammable solvents therefore are required to have continuously operating flammable gas sensors which will send an alarm when vapours are detected. HAL extraction booths provide a visible alarm when concentrations reach 10% of the LEL to allow operators time to change procedures. When concentrations reach 25%, an audible alarm alerts the operator to close valves and evacuate the extraction facility. If previous safety layers fail, operators are warned to evacuate when dangerous levels of gas are detected.
Layer five: use of closed loop extraction equipment
Use of equipment inside the HAL extraction booth that releases flammable solvent vapours directly to the atmosphere without capture is prohibited. In addition, ancillary or support equipment such as air compressors, chillers, vacuum pumps, or heaters can be placed outside of the booth so that those sources of ignition are not inside the work area rated for use with flammable solvents.
Layer six: integrated ventilation controls
The use of controls that integrate the ventilation system with the flammable gas monitor provide an additional layer of safety. The ventilation system exhausts air at a base air flow rate to keep gas concentrations low. However, when the gas sensor detects flammable gas above 10% of the LEL, the ventilation rate is automatically more than doubled to purge the atmosphere within the booth of those flammable gases. When vapour levels fall to safe levels, the ventilation rate resets to the base level. This provides significant energy savings in addition to adding a layer of safety.
Layer seven: fire suppression
All extraction facilities utilising flammable solvents should be equipped with fire suppression systems. Integration of the extraction booth or facility into a building sprinkler system is a cost and system effective approach. If no building sprinkler system is available, the use of a standalone dry powder, carbon dioxide, water mist, or gaseous suppressant system is recommended. Should all else fail, the fire suppression system can prevent spread of a fire beyond the extraction facility.
New Extraction Facility Installation
Planning a new extraction facility is a challenge. Firstly, you will need to identify the market you want to fill. Are you planning to extract CBD oil from hemp, oil from cannabis for vaping, edibles, or concentrates? Will the market you choose support selling raw oil from the extraction process, or will additional purification or concentration be necessary? Do you need high purity out of the extractor, or are you going to de-wax the oil or perform fractional distillation? Are you going to make crystallate? What throughput capacity do you need in terms of pounds of feed material hour?
Answers to these questions will help to choose between extraction processes. Use of carbon dioxide (CO2) as a solvent may result in facility development cost savings, but CO2 extraction systems typically have high equipment costs per unit of output. The use of ethanol as a solvent for extraction can be significantly less costly per unit of output, but the raw oil may be less pure than that produced by CO2. Butane and propane solvent have an intermediate equipment cost per unit of output and can produce high quality oil directly, however they have relatively high facility costs due to the flammability of the solvent. If you choose to make crystallate CBD or THC, pentane is typically used as a solvent, also with relatively high facility costs due to solvent flammability.
Even if you choose CO2, you will likely need to use ethanol as a solvent for post-extraction purification. In summation, if you want to make high quality CBD or THC oil products, you will need to use flammable solvents.
Build-out production facility costs
Design and construction of facilities that use flammable solvents is often two to four times as expensive as other industrial or building space on a cost per square meter basis. Specialised engineers and contractors are necessary to ensure that the facility meets building and fire codes. These specialists design and build each facility on a one-off basis, resulting in high costs.
HAL extraction booth facility costs
HAL Extraction Technology Ltd. developed the HAL extraction booth to simplify the design, construction, and provisioning of facilities for flammable solvents. Use of a HAL Extraction Booth can save 50-70 percent of the overall facility cost. In addition, the HAL Extraction Booth saves energy by having a low base air flow rate, and a higher purge air flow rate only when flammable gases are detected. This can result in operational cost savings and fewer greenhouse gas emissions than a facility that constantly runs at a high air flow rate.
Only the HAL extraction booth has a UL certification for the entire product. Others build booths with certified components but have not had the entire system evaluated by UL. We believe that the HAL extraction booth is closer to UL-Canada, CE, and EXP certifications than any other product. HAL will have those certifications prior to 2022, when widespread European legalisation of cannabis is expected to occur.
HAL has put five times more engineering time into design and development of its products than any of our competitors. HAL is committed to maintaining the technological lead in cannabis extraction facility design and construction and continue supporting our clients, so they provide a safe, effective, and beneficial space for their workers to produce superior products.
HAL Extraction Technology Ltd. has been growing at a breakneck pace to meet the demand for its products. In contrast, Havelick’s retirement plans have not been working out quite as well.
Linn Havelick
Founder
HAL Extraction Booth
+1 720 504 4726
Info@ExtractionBooth.com
Tweet @HALextraction
https://www.extractionbooth.com/
This article will appear in Health Europa Quarterly Issue 11, which is available to read now.